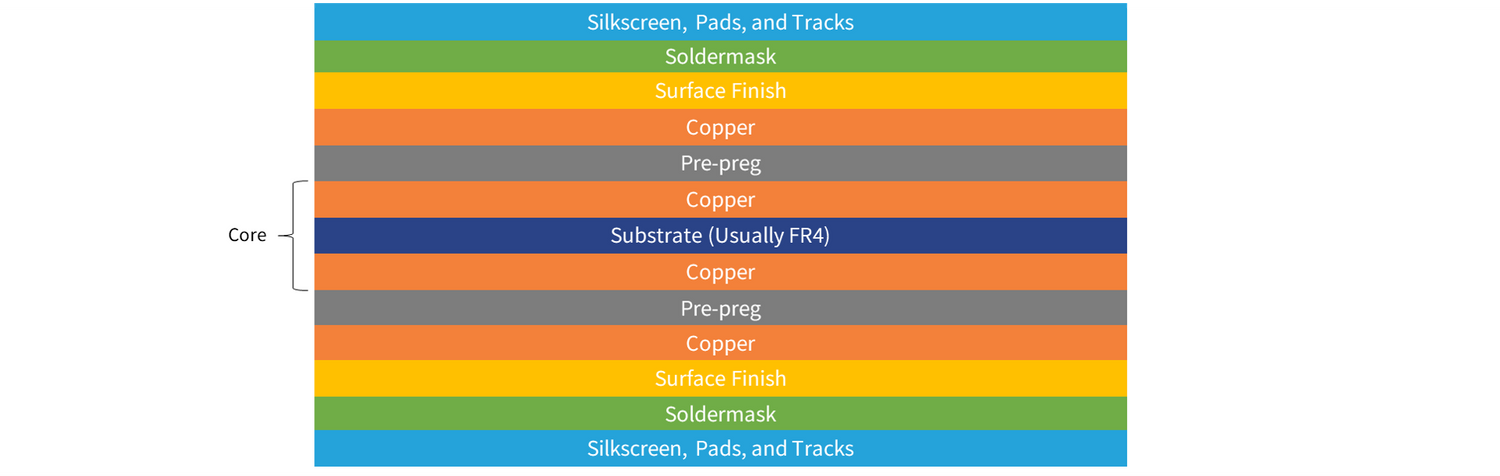
PCB Surface Finish
As different printed circuit boards (PCBs) each have their own specific use, their composition: layers, materials, components, mounting technology, and numerous other processes are different. One of the main differentiating components is the PCB Surface Finish material selection.
The PCB surface finish is done after the PCB fabrication and before the solder mask is applied. PCB surface finish serves several functions, including:
-
Protect the copper circuit against oxidation and corrosion.
Oxidation is fatal for the performance of a circuit board. The oxidized copper will increase the contact resistance between the copper tracks and component leads, and hence reduces the board’s signal integrity.
-
Increase the board’s solderability. Adding a layer of surface finish allows the PCB to achieve the surface flatness required to ease the process of component soldering.
-
The PCB surface finish will give PCBs a clean and shiny surface, which enhances their aesthetics.
As stated before, engineers use different materials to use as a surface finish for different PCBs. Let's dive into the difference between the most commonly used surface finish types: HASL, ENIG, OSP, Immersion Tin, Immersion Silver, and others
-
HASL (Hot Air Solder Levelling)
During the process, molten solder coats the PCB surface, before using hot air to level the surface. The HASL is a lead-based surface finish, so it’s not RoHS compliant. However, there are options for Lead-free HASL which obeys the RoHS compliance.
-
ENIG (Electroless Nickel Immersion Gold)
ENIG means the PCB will be first coated with a layer of nickel, before being layered again with gold.
-
OSP (Organic Solderability Preservative)
OSP uses organic ‘solder’ which is more environmentally friendly than the other surface options. However, the surface is not suitable for multiple reflow processes. OSP is RoHS compliant most of the time, but some traces of hazardous materials might be present when the process is not done carefully.
-
Immersion Tin (ImSn)
Hate it or love it, the Immersion Tin has been one of the most common surface finish options to use. It’s very fit for through-hole applications but has a relatively short shelf-life of 3-6 months. It’s also very prone to whisker growth, so you should put extra care when conducting its following processes, and avoid high temperatures to prevent damage.
-
Immersion Silver (ImAg)
Like immersion tin, immersion silver is done by coating the copper pads with a thin layer of silver. It’s slightly more costly, but the immersion silver surface finish is more robust — its thickness (it’s 4 times thicker than immersion silver for the s allows the circuit board to have more signal integrity.
-
Hard Gold
Hard gold is similar to ENIG, in the sense it covers copper pads with a layer of gold. However, the gold used in hard gold is thicker than ENIG, so it’s more costly. The hard gold PCB surface is very corrosion-resistant. It’s very suitable for high-wear applications, such as connectors and switches. As long as the gold plating solution used in the process is free of prohibited substances, the hard gold surface is RoHS compliant.
-
ENEPIG (Electroless Nickel Electroless Palladium Immersion Gold
ENEPIG, like its name, deposits first a layer of nickel, then a layer of palladium on top of it, before finally finishing it with a layer of gold on the copper pads. ENEPIG provides the best quality PCB surfaces, but it’s also relatively more expensive than the other processes.
Read more to see how each PCB surface treatments compare to each other from: https://www.nexpcb.com/blog/pcb-surface-finish